How will global steel industry advance toward hydrogen-based iron production?
...
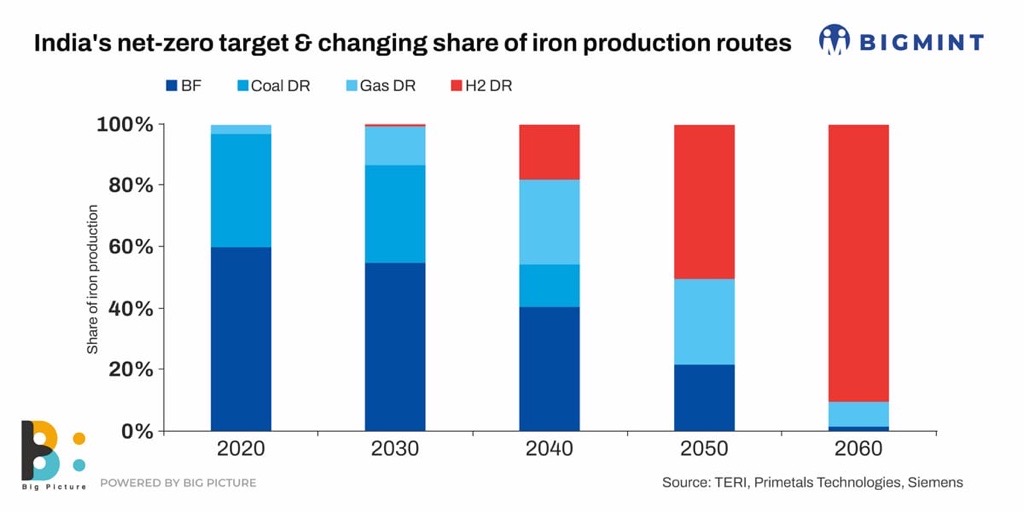
- EU leads the way in NG/H2-based DRI capacity addition
- Cost factor key hurdle in hydrogen adoption globally
- In India, NG-DRI to replace coal-based rotary kilns in short term
Morning Brief: Deep decarbonisation of the global steel industry is not possible without the eventual transition away from fossil fuels to renewables and, especially, hydrogen (H2). However, there is a tendency to think that H2-based technologies are far out into the future and will take a long time to materialise. This may not always be the case.
For example, ArcelorMittal has raked in nearly EURO 2 billion in subsidies from the French, German, and Spanish governments to make the transition away from coal-guzzling BF-BOF technology to NG (and eventually H2)-based DRI technologies paired with EAF to advance decarbonisation goals.
H2 Green Steel has already pre-sold 1.5 million tonnes (mnt) of very low-CO2 steel in 7-year offtake agreements with buyers willing to shell out a premium even before the commencement of commercial operations.
And it is not just in Europe that H2-based DRI is making progress. The conditions that are required to facilitate a smooth transition to H2-DR technology are:
- Declining levelised cost of electricity generated from renewables
- Increasing scale of H2 production
- Emerging carbon markets and taxes
- Preferential demand for low-CO2 steel from government and private sectors
H2 in steel decarbonisation
- Using global average grid power for electrolysis, using H2 instead of coke will significantly lower the carbon intensity of the steel-making process.
- In many developed economies where power grids have less CO2-intensive generation sources, electrolysis can immediately start decarbonising this 'hard-to-abate' industry.
- For economies with a large portion of coal power in their grid, like India and China, H2 can still reduce emissions in the steel industry, even if produced via coal gasification.
Research by the HYBRIT partners, working on a pioneering H2-DR technology, shows that a BF emits 1,600 kgCO2 from the combustion of coking coal and oil to produce one tonne of crude steel. The DRI route only emits 25 kgCO2 while consuming approximately 58 kg of hydrogen, in turn using 2,633 kWh of power.
While the BF-BOF route has a CO2 intensity of over 2 tCO2/thm (tonne of hot metal) and the natural gas (NG)-DR-EAF route emits around 0.8 tCO2/thm, H2-DR paired with EAF steelmaking emits just over 0.1 tCO2/thm.
In contrast with land transportation or shipping or even as a source of industrial heat, the potential of H2 to cut emissions in the steel sector is the highest as it is used not just as a fuel but also a reductant.
Cost factor key
Some companies are developing and deploying breakthrough H2 reduction technology, virtually eliminating direct GHG emissions from the ironmaking process. Key projects include HYBRIT (SSAB/LKAB/Vattenfall) and ArcelorMittal's Hamburg pilot project.
Another group of steelmakers are looking at the transitional use of H2 by blending it with fossil-based reductants, using it in conventional steelmaking processes (BF and DRI) to improve GHG efficiency. Tenova, Salzgitter and thyssenkrupp have or are testing NG-based DRI with high levels of H2 blending. In the BF, blending tests are characteristic of Japan's COURSE50 programme, while thyssenkrupp in the EU and Tata Steel in India have conducted similar pilots.
However, ArcerlorMittal's CEO of European operations, Geert Van Poelvoorde, has recently said in an interview that H2 use in the company's European operations is unviable at present due to cost considerations. H2 prices in the EU, even factoring in the carbon price, are unviable in terms of competition at present. This means higher H2 blending rates and eventual transition to H2 may get delayed indefinitely amid prospects of DRI and clean energy imports from the Middle East and Africa.
IEA analysis has found that the cost of producing H2 from renewable electricity could fall 30% by 2030 as a result of declining costs of renewables and the scaling up of H2 production.
Where does India stand?
India is the world's top DRI producer but the transition to low-CO2 DRI will be a lot slower compared with other parts of the world. A recent study has found that in India gas-based DR plants will be installed during the 2020s, primarily using NG. Limited domestic gas supplies would mean imports would need to increase, with some support provided to steel producers given the higher prices.
When low-cost H2 is available, these plants can switch over to H2. From 2030 onwards, a TERI study observes, DR plants using high shares of green H2 will be constructed. The existing BFs will be decommissioned as they reach the end of their economic life. By 2060, the BFs that remain would need to be fitted with carbon capture technology.
Coal-based direct reduction units have a shorter lifetime versus BFs and so, in this scenario, these units are likely to be phased out before 2050, with NG and H2-based DRI units being deployed in their place.