Expanding frontiers in iron-making technology and steel industry transition -A BigMint report
...
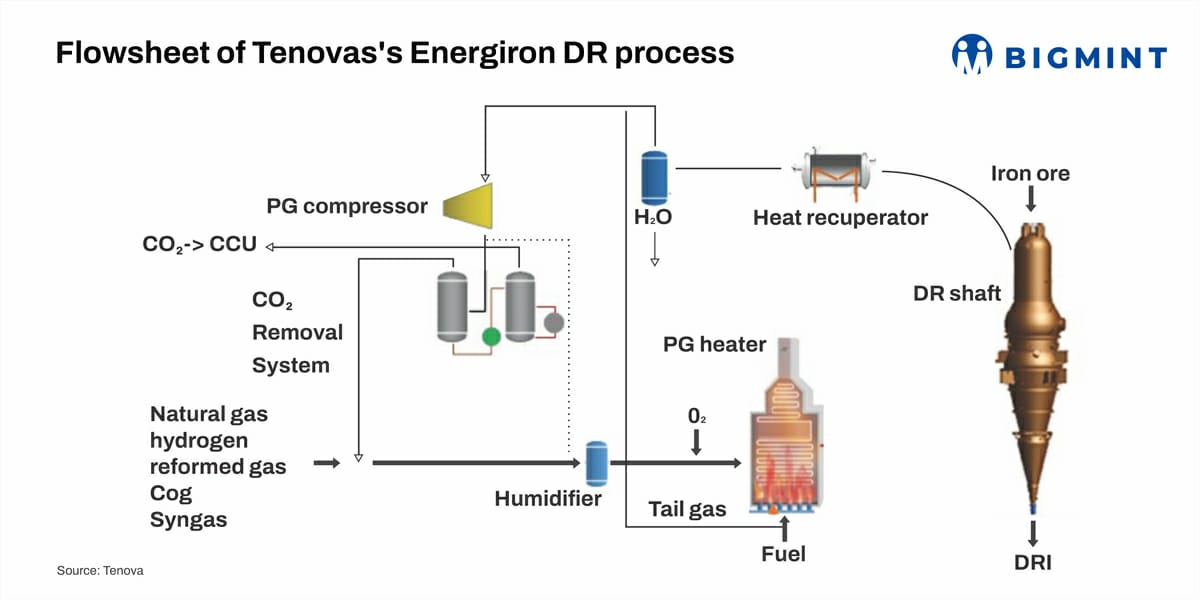
- Decarbonisation of iron-making key to reducing industry emissions
- Innovative DR-smelter processes to make use of sub-par iron ore
- New tech promises integration with existing assets, BF substitution
Morning Brief: While some steel decarbonisation pathways hinge on carbon capture and subsequent storage and utilisation (CCUS) and the circular economy, there are other pathways which offer a direct way of avoidance of carbon emissions, also known as carbon direct avoidance (CDA).
In the conventional BF-BOF steelmaking process, the iron-making zone in the BF accounts for around 70% of process emissions, which signifies that decarbonisation of the steel sector, will have to move beyond traditional iron-making processes, while at the same time making optimum use of globally available raw material reserves.
In the realm of reduction of emissions directly related to iron-making, the basic technological configuration starts with the natural gas (NG)-based DRI iron-making scheme in combination with EAF or melter, with the progressive use of green hydrogen (H2) as replacement of, or integration into, existing BF-BOF installations.
However, the challenges are mainly related to availability of high-grade iron ore for EAF and green H2 supply at required volumes and costs, depending on levelised prices of electricity.
Innovative DR process
The ENERGIRON DR process, a technology jointly developed by Tenova HYL with Danieli, is a flexible scheme in terms of using different reducing gases with the same configuration, process efficiency and CCU system.
It is an adequate scheme for the sustainable production of suitable DRI quality for steel production via EAF or hot metal (HM) via melter, open slag bath furnace (OSBF), using NG and/or H2 as energy replacement for coal.
Key features:
"The Energiron process has the flexibility of direct replacement of NG with H2 in any proportion and in reversible operating mode, with the same configuration and plant equipment, with just minor provisions in some equipment specifications. It has the lowest CO2 emissions not only due to higher efficiency but also due to inherent CCU possibility," informs Praveen Chaturvedi, VP and Head-Sales Upstream India, Tenova Technologies Pvt. Ltd.
The process has a long-lasting experience for using H2 in 70% volume in industrial operating plants, enhanced by demonstration plant campaigns since the 1990s while processing less then 90% vol. of H2.
The energy consumption of the process with 100% H2 is as low as 6.6 GJ/tDRI as H2 for process plus 1.6 GJ/tDRI of fuel and about 25 kWh/tDRI for the core plant.
The process is a DR technology capable of producing hot/cold DRI (HDRI/CDRI) with >4%C (carbon) when using 100% NG. This unique high-C DRI has advantages in terms of reduced power consumption in the EAF and is also tailor-made for production of hot metal in the OSBF.
BF substitution
The scheme consisting of Energiron plant for DRI feeding in the OSBF (Tenova iBLUE scheme) combines production of DRI using NG and H2 and low-grade iron ore pellets with electric arc melter to produce hot metal and granulated slag, as a proven technology to substitute the BF, while significantly reducing CO2 emissions and keeping existing BOFs in operation.
"While the EAF operates under oxidising conditions, in the OSBF the DRI is melted in a reducing environment, which allows for modifications in the slag chemistry, to be suitable for granulation and for use as a by-product in the cement industry," says Chaturvedi.
This scheme is H2-ready for the gradual switch from NG towards further reduced carbon footprint from hot metal to steel, using H2 in the direct reduction plant. Due to the process conditions of Energiron technology, even with 35% H2 as process energy (or 65% vol.), it is possible to produce DRI with 3.3%C and thus 4% in hot metal with carburisation balance in the OSBF, he adds.
Technology adoption
In March 2022, China's Sinosteel Engineering & Technology Co. Ltd. contracted Tenova for the design and supply of a H2-based 1 mnt/year CDRI Energiron plant with preparation for HDRI production
In November 2020, major Chinese steelmaker HBIS Group roped in Tenova for the implementation of the Paradigm Project, a High-Tech Hydrogen Energy Development and Utilization Plant. The project includes a 600,000 t/year DRI plant
In August 2022, Tata Steel Netherlands awarded Energiron the Heracless (Hydrogen-Era-Carbon-Less) project, aiming to transition the integrated steel mill in IJmuiden from the current BF-technology to green H2-based steel production
In October 2022, ArcelorMittal contracted Tenova for the design and supply of a H2-ready 2.5 mnt/year Energiron plant for its Dofasco plant in Canada