Chinese steelmakers optimising ore mix to cut costs
...
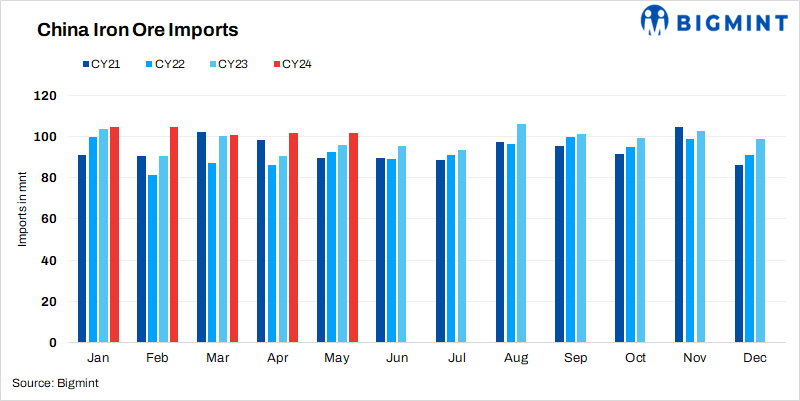
Many Chinese steel mills are now exploring different ore blending strategies to reduce their production costs during the steelmaking process, and for some, their efforts have paid off, Mysteel Global learned from the Bohai Rim Steelmaking Raw Material Industry Development Conference held in North China's Tianjin over 3-4 July.
"When faced with the challenge of losses or low profit margins in steel production - which occurs quite frequently these days- steelmakers usually take some measures to lower their costs including keeping low stocks of raw materials, producing only based on orders at hand, and also seeking more cost-effective feeds," said Liu Chuanchuan, a senior engineer from Hangang Nengjia Steel Co., Ltd.
In recent years Hangang Nengjia, a steelmaker based in Handan city in North China's Hebei province, has used more low-grade limonite, like Yandi Fines and FMG Blended Fines, to replace high-grade hematite, according to Liu. "The ratio of these low-grade ores used in our blast furnaces has risen from 10% to 30%, as their good assimilation can make up for their low grade," he told delegates.
Meanwhile, the company is also favouring lumps - whose price advantage has become clearer in recent years - as well as some non-mainstream ores to lower costs, Mysteel Global noted.
On the other hand, at Shougang Jingtang United Iron & Steel Co, the way of cost-saving is to cut fuel consumption by lifting the ratio of low-silicon pellets, which also contributes to environmental protection, Shougang Jingtang senior engineer Ma Chengwei said at the conference.
"Sintering ore fines are the major feeds in the process of ironmaking, but pellets are more environmental-friendly," Ma explained. For every tonne of raw ore, the pelletising procedure only emits 37% of the carbon dioxide and 55% of other pollutants, compared with those emitted during the sintering process, he said.
Mysteel's tracking of 64 steel mills nationwide showed that over the past two years the portion of pellets used in their blast furnaces fluctuated only between 13.94-16.69%, while Shougang Jingtang is now successful in bringing its pellet consumption ratio up to around 55% after years of research and development, according to Ma.
Other steel companies that have managed to lift their pellet ratio above 50% include Ansteel and Baogang Group, Mysteel Global learned.
Note: This article has been written in accordance with an article exchange agreement between Mysteel Global and BigMint.